A prime example of the success of these innovations is the repeat order by E.B. Bradshaw & Sons, a long-term client who, after six years of operations with the “lights out” Flexy Mill equipped with Direct Drive torque motor technology and the KERS energy recovery system, has decided to renew their trust in Omas for their latest mill. This renewed commitment comes as a result of proven energy management, flour consistency, and optimized production processes, thanks to the innovative belt-free design of the Leonardo rollermill. The KERS (Kinetic Energy Recovery System), which recovers kinetic energy generated during milling, has had a significant impact on reducing energy consumption, contributing to overall operational savings without compromising performance. The efficiency and sustainability of the Flexy Mill have been validated over the long term, leading E.B. Bradshaw & Sons to select Omas as their strategic partner for the future.
Additionally, the Leonardo roller mill, which has demonstrated its ability to save energy for seven years, ensures consistent milling and low maintenance levels. The system’s robustness and reliability, combined with its ability to maintain continuous operation with reduced operational costs, have been key factors in renewing the client’s trust.
E.B. Bradshaw & Sons Ltd, located in Driffield in the East Riding of Yorkshire is a well-respected name in the milling industry with a history dating back to 1890.
Stuart Bradshaw, Joint Managing Director of Bradshaws commented, “we have been family millers for over 130 years, but despite the heritage, we are conscious that we must keep developing our milling facilities to provide both high quality and consistent flours that our marketplace demands. We pride ourselves in that we source much of our 4,000 tonnes a week requirement from local family farms, some of whom have supplied Bradshaws for those 130 years. When the Board decided to add to their milling estate in 2016, we explored several suppliers who could deliver the mill we required. Omas technology was instrumental in our decision to partner with them. Since the Omas mill was commissioned in 2018, we have been delighted with the performance, the energy savings, the reliability and after sales service. To respond to the growth in our customer base, we had no hesitation to entrust our new mill project with Omas. Omas diagram and machine technology is second to none, their installation team and cutting-edge automation provide us with single source responsibility to design and deliver the project on time and in budget. We look forward to the new mill coming on stream later this year.”
Bradshaw’s operations are centered around sustainability and quality, values that resonate with Omas Industries’ mission. Their decision to continue the partnership with Omas is a testament to the success of this collaboration, which has improved not only the energy efficiency of their operations but also the quality of the flour they produce.
E.B. Bradshaw’s long-standing commitment to innovation, coupled with Omas’ technology, exemplifies how the milling industry can evolve to meet modern demands for efficiency, sustainability, and consistent product quality.
The first Omas mill highlighted EB Bradshaw as an industry pioneer. They were the first miller to understand the benefits of direct drive rollermills and to take advantage of the adaptive mill able to set up roll speed and differentials to minimize energy and produce consistent flour at optimum yield.
This drive to push technological barriers will also be respected in the new mill. It will feature the latest HMI/SCADA as well as being the first mill in the word to benefit from the Omas Milling Pilot.
The Milling Pilot is an automated system that monitors and controls all the grinding parameters of the rollermill, minimizing operator intervention to provide fully autonomous operation.
Infrared sensors detect the temperature of the rolls, load cells monitor the roll pressure and ODS provides automatic roll gap control. All of the parameters are controlled, set and monitored via a user friendly interface to provide repeatable and perfectly stable operation, providing energy efficiency and enhancing sustainability.
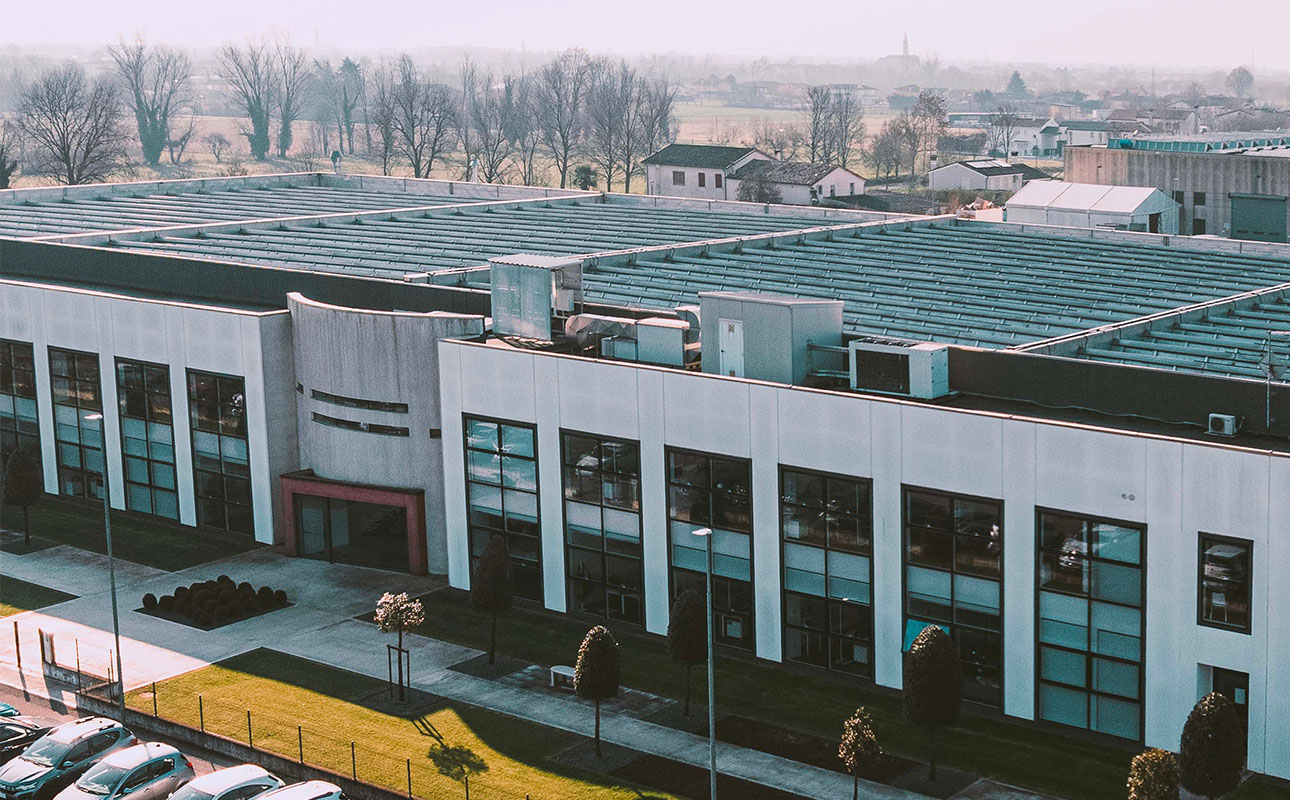