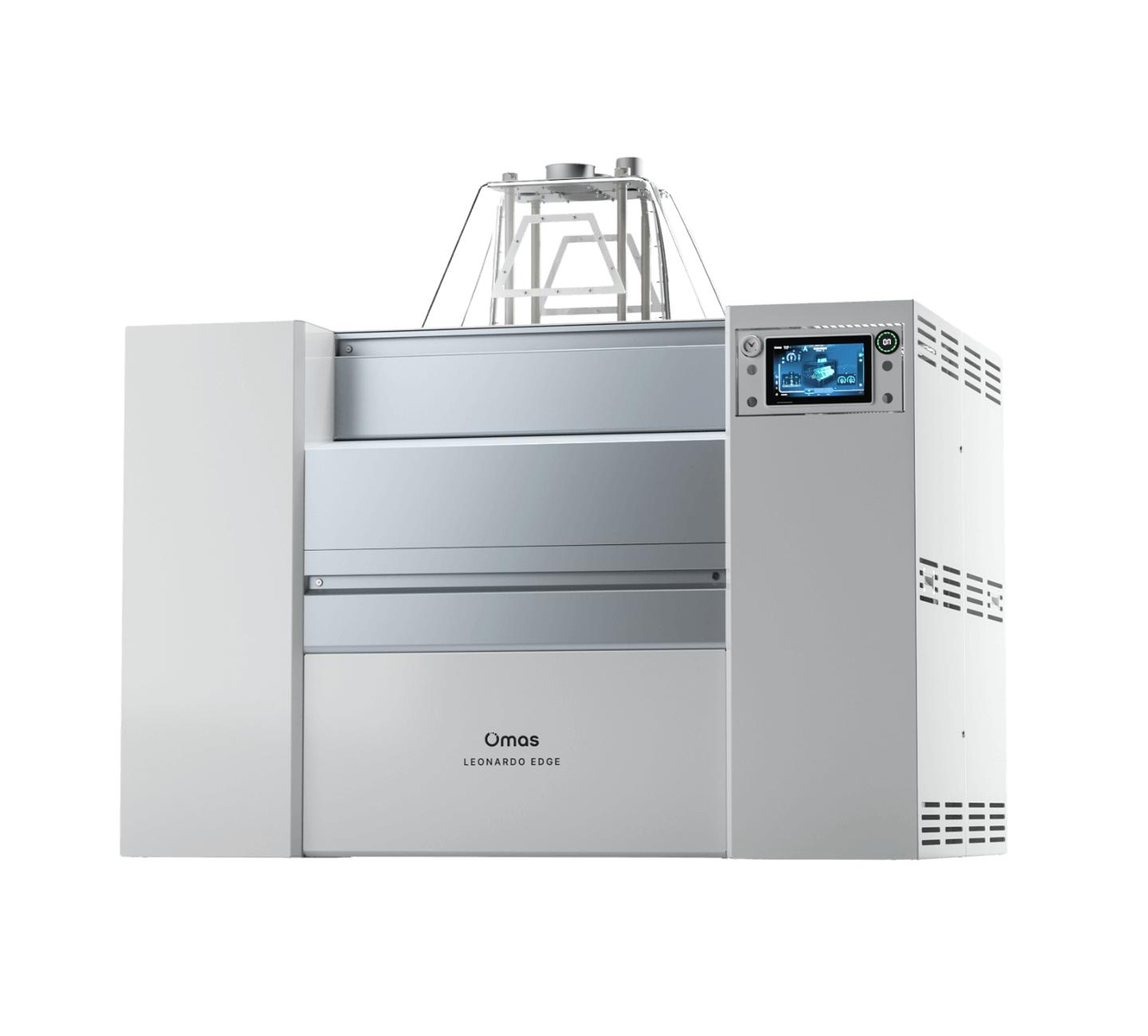
Roller Mill
Grinding
Leonardo Edge
The roller mill is the heart of every milling plant. With the new Leonardo Edge, Omas has redefined industry standards by combining innovation, efficiency, and sustainability. Protected by an international patent, Leonardo Edge pushes the art of milling beyond traditional boundaries: superior performance, maximum energy efficiency, and total process control.
01
Technical features
Grinding performance
Perfect grinding control.
- +15% capacity of the feed hopper
- Infrared sensors for product level monitoring
- Improved access to the feed hopper for quicker and easier cleaning grazie alla finestra di ispezione trasparente
- Gear motor driven by inverter for speed control: RPM controlled via touchscreen
- Roller rotation control sensor
- Easy cleaning of feed rollers with quick access through manually opened door operated by GAS pistons
- Patented technology OKS – Omas KERS System (Kinetic Energy Recovery System)
- 4-8 horizontal rollers for enhanced grinding
- Maintenance: over 90% reduction in time and costs
- Access to grinding parameters via touchscreen panel with adjustment of individual roller speeds from 60 to 550 RPM
- Possibility to reverse cutting-back functions by reversing the slow roller with the fast roller
- Possibility to change the grinding ratio in just a few seconds directly from the touchscreen
- The machine does not require compressed air, which is only needed in case the optional OCS Omas Cylinder System is installed
- Elimination of the motorization plane and simplification of the overall plant layout
- Extreme work safety for operators, as all mechanical movements have been eliminated
- Better living: reduced environmental impact resulting in lower CO₂ emissions
02
research and development
key factors
The technologies that make Leonardo Edge the revolutionary, unique and extraordinary roller mill.
-
TechnologyOMAS PRESSURE SYSTEMA system for controlling and measuring the grinding roller pressure using a load cell device applied directly to the cylinder actuation systems.OPSTechnologyOMAS CYLINDERS SYSTEMRoller temperature control sensor that determines whether the machine is working uniformly across the entire milling surface or needs further calibration.OCSTechnologyOMAS MULTIRECIPEFull recipe control including roll gap, feeding roll rpm, hopper level, individual grinding roll speeds, ratio adjustment and roll inversion, fast roll to slow and vice versa.OMR03FINISHES AND MATERIALSMaterial qualityPETG PolyethyleneFeeding hopper made of robust PETG polyethylene, obtained through a special hot-molding process suitable for food contact. The material’s total transparency allows immediate visual inspection of the product.Anti-wear burnishingSophisticated mechanics made of high-resistance materials heat-treated through an anti-wear burnishing process.Anodized aluminumOur profiles undergo an electrochemical treatment that ensures exceptional surface cleanliness. Thanks to a sound-absorbing filling treatment, we also ensure a significant reduction in vibrations.Carbon steelWe design this special type of welded, painted, and mesh-framed steel to provide higher structural strength and significantly reduce vibrations.04SERVICESELECTRICAL ENGINEERING AND AUTOMATIONWe revolutionize the traditional way of working in the mill, focusing on automation and digitalization of your production processes.Your next plant begins today: let’s build it togetherLet’s collaborate to create a custom system that meets your specific needs. We combine our experience with your vision to develop a functional and efficient solution, designed to last over time.
Sign up for our newsletter
Sign up for exclusive news and industry innovations